Discover how we help our customer avoided costly downtime and saved thousands by choosing the right advice over thicker dies.
The Challenge
Our feedmill customer was facing repeated cracking of their ring dies. Their previous supplier suggested making the die thicker to improve strength. Before placing the order, they consulted with Tien Phat.
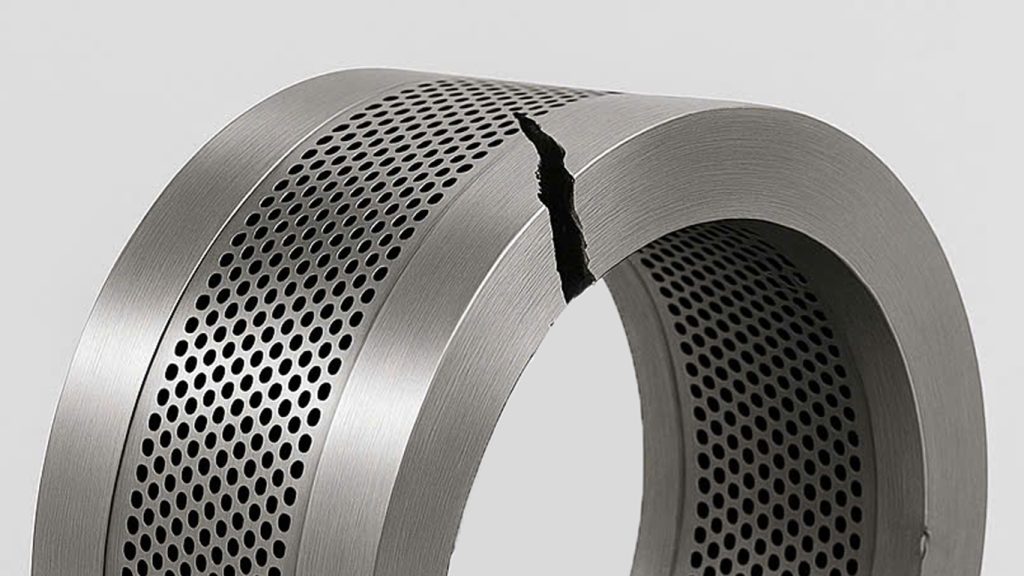
Our Technical Analysis
At Tien Phat, we believe in solving the root cause. We asked the customer to review 3 possible issues:
1. Clogging: | 2. Incorrect ring die setup: | 3. Incorrect roller setup: |
---|---|---|
It is a common cause of ring die cracking and is caused by many other reasons: die quality, raw materials, operation,… | Incorrect ring die installation will cause the machine to shake and vibrate during operation, easily causing the die to break. | Pressing the roller too close to the ring die surface, is also one of the causes of die cracking. |
We explained that just increasing thickness won’t solve these issues – and may result in higher cost without benefit.
The Result
The customer followed our recommendation. After monitoring, reviewing and adjusting their process, they saw:
-
- No more die cracking
-
- Stable pellet output
-
- A full production shift without shutdown
Impressed by the outcome, they placed a large order of custom-made ring dies with us. Our price may not be the cheapest in the market, but they still choose us, because we solved the real problem.
At TIEN PHAT, we don’t just sell parts. We deliver expertise, dedication and real performance.
Experiencing similar issues with your ring dies? Let us help.